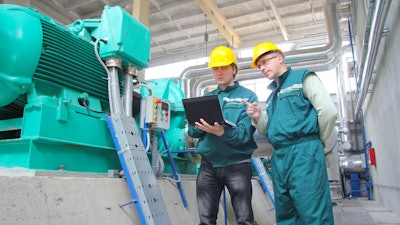
In response to much-welcome hints of growth in the U.S. manufacturing sector, the U.S. Department of Labor has recently announced changes in OSHA operational priorities to address worker safety concerns. The agency’s new regional office in Birmingham, AL will oversee safety compliance across six states plus the Florida panhandle—an area that’s booming with manufacturing jobs, particularly in food processing, construction, heavy manufacturing and chemical processing.
Because these are often hazardous jobs, now more than ever companies need to deploy every safety feature at their disposal to protect workers, mitigate risk and to help overcome the perception of manufacturing as dangerous work to aid in recruiting and retention of skilled workers.
Despite the need to make safety a priority, some manufacturers fail to fully capitalize on key safety features in common industrial equipment, either due to lack of awareness or lack of prioritization. When the primary goal is to simply keep equipment running to meet production targets, the status quo often takes over, leaving human well-being compromised.
The attitude of “if it is not broke, don’t fix it” can be a dangerous mentality when it comes to safety. It can be hard to justify investing time in changing standard operating procedures (SOPs) and implementing new features when your operation has been running fine without them.
Unfortunately, there is no way to prevent all safety risks. Accidents can happen when they’re least expected. However, risk mitigation helps to identify potential risks ahead of time and institute plans to prevent accidents. When you’re dealing with expensive, heavy-duty industrial equipment, there’s no reason not to maximize that investment by taking advantage of every single feature that can keep the equipment, and more importantly, the equipment operators, safe.
Now is the perfect time to consider these six strategies for taking full advantage of equipment safety features.
- Conduct an equipment inventory audit. You can’t use safety features you don’t know you have. Start by conducting a facility wide inventory of all equipment, including an audit of the safety features inherent in each one. Figure out what’s being used, whether it’s being used properly or to its full capabilities and create an equipment plan for utilizing the safety features on all of your assets. Work closely with equipment manufacturers to fully understand the capabilities of the safety components included so you can make the most of your investment.
- Check your lights. Chances are, if you’re still running conventional HID lighting, it’s becoming a safety risk. Dirty power can take a serious toll on lighting which manifests as frequent flicker and surges as heavy machinery cycles on and off. This can cause unexpected lighting failures that plunge critical areas into sudden darkness, raising the risk of trips, falls, and unintentional contact with fixed objects and machinery. Not to mention, the dingy orange glow of HID that distorts colors and frequent maintenance, adding to the safety concern. Upgrading to crisp, modern lighting such as industrial LED fixtures can reduce the risk of accidents by as much as 60 percent. They’re also much more tolerant of dirty power, dramatically reducing maintenance and the risk associated with working at heights.
- Get connected. Detecting out-of-spec operation of equipment before an incident occurs can dramatically improve safety. Modern Industrial Internet of Things (IIoT) technology allows facilities to leverage Programmable Logic Controller (PLC) integration to monitor for issues and predict maintenance needs. A multitude of systems can now be integrated with PLC platforms, allowing for data collection on equipment usage and safety incidents to identify patterns and areas of improvement. This integration is ideal for LED lighting, HVAC, ventilation and air quality monitoring systems and large industrial machinery, allowing site managers to monitor for and receive alerts and notifications of any anomalies or maintenance needs before they create a risk. It also can provide predictive analytics to help spot potential safety issues before they happen.
- Don’t ignore preventative maintenance. Unplanned outages and major equipment repairs are high-risk situations. Especially if safety equipment is broken yet the machine still functions. It's easy to ignore those mangled or missing guards, shields and other accident prevention features. Conduct routine inspections on all equipment and prioritize critical machinery components, such as engines, emergency shut-offs and other safety features to prevent premature failures and accidents. The cost of an accident—both financially and the human toll—far outweighs the cost of taking the time to inspect and repair proactively.
- Can you see me now? Most equipment comes with safety stickers, signage and color-coded labeling to warn operators of risks and ensure proper protocol in operations. But if those are covered in dirt and grease, it’s impossible to see them clearly. Not to mention, not having them visible could lead to some hefty fines. As part of PM procedures, make sure those placards are visible, legible and clear to the viewer.
- Plan for emergencies. Most facilities have emergency and evacuation plans, but don’t fully leverage the capabilities of plant equipment to aid in safety. For example, in the event of a power outage, LED lighting is much more compatible with battery backup electricity due to its low-wattage consumption. That means the LED lights can run longer and brighter than conventional lighting on the same power source.
LED lights can also be programmed to illuminate paths to safety and move workers away from hazardous conditions. When integrated with air quality monitoring, this system can provide dynamic illumination—monitors that detect airborne hazards shut lights off while those that don’t detect contamination turn lights on, guiding employees out of harm’s way.
Employee safety should always be every company’s number one priority, and most manufacturers invest heavily in safety planning, special equipment and protocols, when in fact, the best investment may have already been made. Simply leveraging the full capabilities of common manufacturing equipment can dramatically reduce the risk of accidents and make facilities safer, more efficient and more attractive places to work.