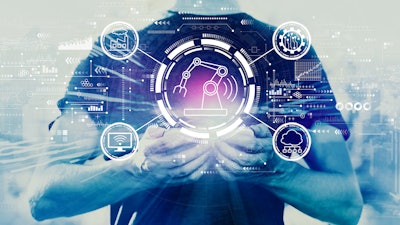
After taking a hit due to rising interest rates, increased production activity is creating an urgent need for more workers on the shop floor. In fact, The Manufacturing Institute reports that the U.S. manufacturing is expected to increase by 3.8 million workers over the next decade.
The expected influx of new workers presents a host of new safety challenges. In this historically high-risk industry, safety must remain a number one priority. Here’s how manufacturing leaders can prepare for a worker influx without a subsequent increase in injuries.
Building a Foundation
The combination of inexperienced workers, resource strain, and shifting dynamics can contribute to a rise in worker injuries during periods of hiring influx. However, when an organization prioritizes a strong safety culture and management system, it’s much easier to weather these growing pains.
Safety requires engagement from everyone in the organization. Whether a brand-new employee or a C-suite executive, active participation to reduce injuries should be a non-negotiable priority. An engaged workforce can have up to 48 percent fewer safety incidents. So how can leaders engage their workforce so everyone is accountable and active in working toward safety goals?
At leading companies, one common characteristic is facilitated employee engagement, including introduction and onboarding of new employees to a streamlined and intuitive concern (or “good catch”) reporting process made possible by technology. New and tenured employees should feel empowered and capable of reporting concerns, near misses, and incidents as soon as they happen.
Accessible and ubiquitous technologies like mobile/tablet-based interfaces and advanced technology can make the process easy and seamless, which makes employees more likely to actively identify potential risks and contribute to a safer work environment. Compliance and hazard-specific awareness training are another key component of creating a safety culture. This enables companies to provide comprehensive safety training to employees to develop their safety knowledge and skills, fostering an environment of continuous learning and improvement.
A strong safety culture and management system that connects people and process to organizational objectives are the foundation of a strong Environmental Health and Safety (EHS) program. By equipping workers with fit-for-purpose technology, organizations can bring their safety culture to the next level.
Elevating Safety Practices
AI and other advanced technologies are transforming the way we work and live, but in industries like manufacturing, they are quite literally saving lives. When used correctly, they have the power to improve an organization’s safety culture by making injury prevention easy and attainable.
- Artificial Intelligence. In manufacturing, AI is pivotal in enhancing insights, boosting productivity, and supporting real-time decision-making to ensure workplace safety. It can also streamline data processing of concern reports (or “good catches”), near misses, and incident reports by intaking, summarizing, and acting upon large volumes of data. Leaders can identify trends and indicators of potentially serious incidents (PSIs) by allowing AI to quickly analyze datasets. This enables teams to put proactive measures in place and improve the quality of data that is being collected to ensure incidents and injuries are being reported thoroughly and accurately. This can include prompting employees to share additional details about incidents, such as how high a fall was, what chemical was spilled, or which machine is malfunctioning. This level of detail not only saves time, but also strengthens EHS programs as a whole.
- Computer Vision & Wearables. Computer vision systems with advanced cameras and machine learning algorithms can monitor factory floors or work areas in real time. The tech is able to identify potential hazards and unsafe behaviors far faster and more extensively than a human could. It even enables manufacturers to detect anomalies such as equipment malfunctions, unauthorized personnel in restricted areas, or workers engaging in risky activities. This is priceless when there’s an influx of people, which can make it more difficult for management to have a complete picture of what’s happening on the factory floor. Wearable devices are another technology transforming safety for workers in manufacturing – no matter the volume. This includes tools like smart helmets, safety vests, or watches that can provide workers with real-time feedback on their environment and personal health metrics.
- Mobile Technology. Mobile technology has revolutionized incident and risk reporting for large workforces, offering unparalleled convenience and efficiency. Instead of using a shared computer or document, mobile applications enable employees to report incidents directly from a personal mobile device. This means workers can quickly document safety concerns and hazards they encounter on the factory floor in real time. Issues can then be addressed promptly, instead of at the end of a shift, minimizing the risk of accidents and injuries. Mobile technology for incident reporting allows manufacturing companies to foster a culture of safety, empower employees to actively participate in near miss identification and mitigation, and ultimately create safer work environments for all.
As the manufacturing industry experiences a surge in workforce numbers, prioritizing safety is not merely important—it's non-negotiable. By fostering a strong safety culture, investing in management systems, and embracing technologies like AI, computer vision, wearables, and mobile reporting, companies can mitigate risks and save lives on the factory floor.
Safety should never be an afterthought—it's the cornerstone of success.